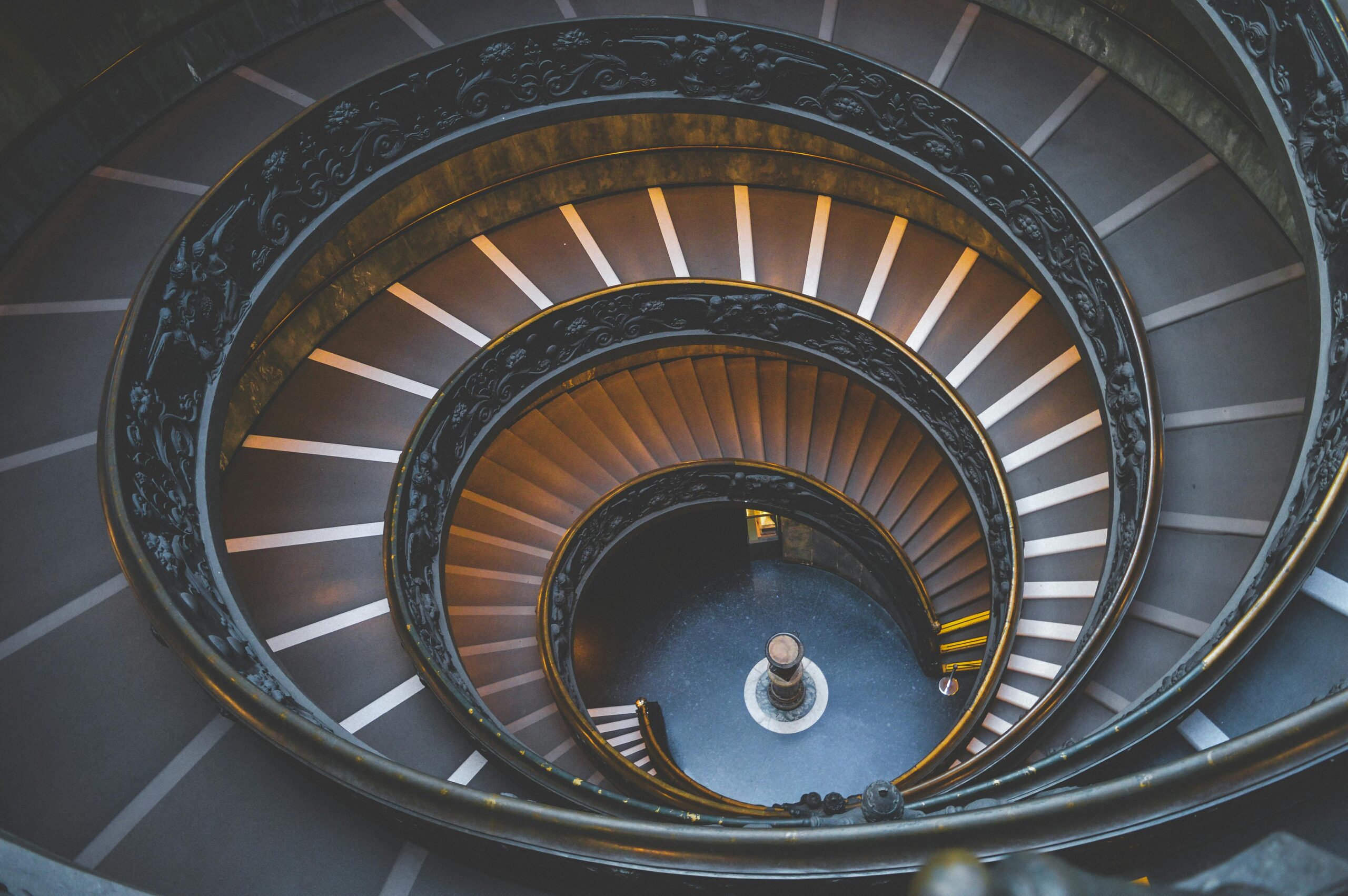
Achieving Circularity: Perspectives from the Heavy Industry
by Paul McIntosh
Circularity, the principle of designing systems that minimize waste and make the most of resources, is becoming increasingly critical in heavy industry sectors such as building materials, automobiles, mining, chemicals, construction, shipbuilding, aerospace, and energy. The traditional linear economy model—take, make, dispose—leads to significant environmental degradation, resource depletion, and economic inefficiencies. Transitioning to a circular economy involves rethinking production and consumption patterns to create closed-loop systems where materials are reused, recycled, and regenerated. This article explores the principles and applications of circularity in these heavy industries, highlighting successful examples and offering insights into future developments. However, there is more to be done in this sector with innovation, collaboration and investment being key to facilitate faster and smarter transitions.
Circular Economy Principles: The circular economy is based on three core principles:
1. Design Out Waste and Pollution: Products are designed to prevent waste and pollution, considering the entire lifecycle from material sourcing to end-of-life disposal.
2. Keep Products and Materials in Use: Through strategies like reuse, repair, remanufacture, and recycling, products and materials are kept in circulation for as long as possible.
3. Regenerate Natural Systems: Circular systems aim to restore and regenerate natural ecosystems rather than deplete them.
Circularity in Building Materials and Construction
Challenges and Opportunities: The construction industry is one of the largest consumers of raw materials and a significant producer of waste. Traditional construction practices often involve the use of non-renewable resources and generate considerable amounts of waste during demolition. However, the industry also presents numerous opportunities for implementing circular principles.
Key Strategies
Reuse and Recycling of Materials: The reuse and recycling of building materials are fundamental to circular construction. This involves reclaiming materials from demolition sites for use in new projects, thereby reducing the need for virgin materials and minimizing waste. For example, reclaimed bricks, timber, and steel can be used in new constructions, maintaining structural integrity while reducing environmental impact (Adams et al., 2017).
Modular Construction: Modular construction involves designing buildings in such a way that components can be easily assembled, disassembled, and reused. This approach not only facilitates the recycling of materials but also allows for greater flexibility and adaptability in building designs. Prefabricated components can be manufactured off-site and transported to the construction site, reducing waste and improving efficiency (Guglielmo, 2018).
Sustainable Material Innovation: Innovating with sustainable materials is another key strategy. This includes the development and use of bio-based materials, such as hempcrete and bamboo, which are renewable and have lower environmental impacts compared to traditional materials like concrete and steel. Additionally, advancements in material science have led to the creation of self-healing concrete and other smart materials that extend the lifespan of buildings and reduce maintenance needs (Van Damme et al., 2020).
Examples:
The Ellen MacArthur Foundation’s Circular Buildings Toolkit: The Ellen MacArthur Foundation has developed a Circular Buildings Toolkit that provides guidelines and best practices for designing and constructing circular buildings. The toolkit emphasizes the importance of material passports, which document the properties and origins of building materials to facilitate their reuse and recycling at the end of a building’s life (Ellen MacArthur Foundation, 2019).
Park 20|20 in the Netherlands: Park 20|20, located in the Netherlands, is an example of a successful circular building project. This business park is designed according to circular economy principles, using cradle-to-cradle certified materials and incorporating renewable energy systems. Buildings in Park 20|20 are constructed to be fully disassemblable, ensuring that materials can be reused or recycled at the end of their lifecycle (Van Timmeren & Jansen, 2016).
Circularity in the Automobile Industry
Challenges and Opportunities: The automobile industry faces significant challenges in terms of resource consumption and waste generation. Traditional car manufacturing relies heavily on finite resources such as metals and fossil fuels, and end-of-life vehicles contribute to substantial waste and environmental pollution. However, the sector also presents unique opportunities for circularity through the adoption of innovative business models and technologies.
Key Strategies
Design for Disassembly: Designing vehicles for disassembly involves creating car components that can be easily taken apart and recycled or reused. This approach facilitates the recovery of valuable materials at the end of a vehicle’s life, reducing the demand for virgin resources and minimizing waste. For example, BMW’s i3 electric car is designed with modular components that can be easily disassembled and recycled (Kümmerer et al., 2020).
Remanufacturing and Refurbishing: Remanufacturing and refurbishing extend the life of vehicle components by restoring them to like-new condition. This not only conserves resources but also offers economic benefits by reducing the need for new parts. Companies like Caterpillar and Volvo have established remanufacturing programs that refurbish engines and other components, offering them at a lower cost compared to new parts (Lund & Hauser, 2019).
Car Sharing and Mobility Services: Shifting from ownership to access-based models, such as car sharing and mobility services, can significantly reduce the number of vehicles on the road and the associated environmental impacts. Car sharing platforms like Zipcar and mobility services like Uber promote the efficient use of vehicles, reducing the need for new car production and lowering overall resource consumption (Cohen & Kietzmann, 2014).
Examples
Renault’s Circular Economy Program: Renault has implemented a comprehensive circular economy program that includes vehicle design, manufacturing, and end-of-life processing. The company’s Re-Factory in Flins, France, is dedicated to the remanufacturing and recycling of vehicles and parts. This facility aims to process over 100,000 vehicles annually, recovering valuable materials and reducing waste (Renault Group, 2021).
Tesla’s Battery Recycling Initiatives: Tesla has developed a closed-loop battery recycling system to recover valuable materials from used batteries. The company’s Gigafactory incorporates battery recycling processes that recover metals like lithium, cobalt, and nickel, which are then reused in new batteries. This approach not only conserves resources but also reduces the environmental impact of mining and processing raw materials (Tesla, 2020).
Circularity in Mining
Challenges and Opportunities: The mining industry is essential for extracting the raw materials needed for various sectors, including construction, energy, and manufacturing. However, traditional mining practices often result in significant environmental degradation, including habitat destruction, water pollution, and high carbon emissions. Implementing circular economy principles in mining can mitigate these impacts and enhance resource efficiency.
Key Strategies
Mine Tailings Reuse: Mining operations produce vast amounts of waste, known as tailings, which can pose significant environmental risks. Reprocessing mine tailings to extract additional minerals and using them as raw materials in construction and other industries can reduce waste and environmental impact (Golev et al., 2014).
Eco-Friendly Mining Technologies: Adopting eco-friendly mining technologies, such as in-situ leaching and biomining, can minimize environmental damage and improve resource recovery rates. These technologies reduce the need for large-scale excavation and lower the environmental footprint of mining operations (Brierley, 2010).
Circular Mining Business Models
Developing circular business models, such as product-as-a-service and extended producer responsibility, encourages mining companies to design products with end-of-life recovery in mind. This approach can enhance material recovery and recycling, reducing the need for new mining activities (Despeisse et al., 2017).
Examples
Boliden’s Aitik Mine: Boliden’s Aitik mine in Sweden has implemented innovative waste management practices to reduce environmental impact. The mine reprocesses tailings to extract additional minerals and uses waste rock for construction materials. Boliden’s approach demonstrates the potential for circularity in mining operations (Boliden, 2020).
Rio Tinto’s Aluminium Recycling: Rio Tinto, one of the largest mining companies, has developed a closed-loop aluminium recycling process. By recycling aluminium scrap, the company reduces the need for bauxite mining and lowers greenhouse gas emissions. This initiative aligns with Rio Tinto’s commitment to sustainability and circular economy principles (Rio Tinto, 2021).
Circularity in Chemicals
Challenges and Opportunities: The chemical industry is a major contributor to global resource consumption and environmental pollution. Traditional chemical production processes often rely on non-renewable resources and generate hazardous waste. Implementing circular economy principles can transform the industry, making it more sustainable and resource-efficient.
Key Strategies
Chemical Recycling: Chemical recycling involves breaking down plastic waste into its basic chemical components, which can be used to produce new plastics and chemicals. This process can handle mixed and contaminated plastics that are not suitable for mechanical recycling, reducing plastic waste and dependence on virgin materials (BASF, 2020).
Bio-Based Chemicals: Developing bio-based chemicals from renewable resources, such as agricultural waste and algae, can reduce the environmental impact of chemical production. Bio-based chemicals offer a sustainable alternative to fossil fuel-derived products and contribute to the circular economy by utilizing waste streams (Ghisellini et al., 2016).
Closed-Loop Systems: Implementing closed-loop systems in chemical production involves designing processes that recover and reuse chemicals and by-products. This approach minimizes waste and resource consumption, enhancing the sustainability of chemical manufacturing (Zimmermann et al., 2020).
Examples
BASF’s ChemCycling: BASF’s ChemCycling project focuses on chemical recycling of plastic waste. The process converts mixed and contaminated plastics into pyrolysis oil, which can be used as a feedstock for producing new chemicals and plastics. This initiative demonstrates the potential for circularity in the chemical industry (BASF, 2020).
Braskem’s Green Polyethylene: Braskem, a Brazilian chemical company, produces green polyethylene from sugarcane ethanol. This bio-based plastic reduces greenhouse gas emissions and reliance on fossil fuels, contributing to the circular economy. Braskem’s green polyethylene is used in various applications, including packaging and consumer goods (Braskem, 2019).
Circularity in Shipbuilding
Challenges and Opportunities: The shipbuilding industry is resource-intensive, consuming large amounts of steel and other materials. Ships also have long lifespans, and their end-of-life disposal can be environmentally damaging. Implementing circular economy principles in shipbuilding can reduce resource consumption and environmental impact.
Key Strategies
Ship Recycling: Ship recycling involves dismantling ships at the end of their service life and recovering valuable materials for reuse. This process reduces waste and conserves resources. However, traditional shipbreaking practices can be hazardous and environmentally damaging. Implementing safe and environmentally sound recycling practices is essential (Andersen, 2001).
Modular Ship Design: Designing ships with modular components that can be easily replaced, upgraded, or reused can enhance the sustainability of shipbuilding. Modular design facilitates repairs and upgrades, extending the lifespan of ships and reducing the need for new materials (Thomson et al., 2016).
Green Shipbuilding Technologies: Adopting green shipbuilding technologies, such as energy-efficient propulsion systems and eco-friendly materials, can reduce the environmental footprint of ships. Innovations like air lubrication systems, which reduce hull friction and fuel consumption, contribute to more sustainable shipbuilding (Schlüter et al., 2014).
Examples
Maersk’s Ship Recycling Program: Maersk, a global leader in shipping, has implemented a responsible ship recycling program. The company ensures that its ships are recycled in facilities that meet high environmental and safety standards. Maersk’s approach demonstrates the potential for circularity in shipbuilding and end-of-life disposal (Maersk, 2019).
Damen’s Modular Ship Design: Damen Shipyards Group has developed a modular ship design concept that allows for easy customization and upgrades. The modular approach enables components to be replaced or upgraded without the need for extensive retrofitting, extending the operational life of ships and reducing resource consumption (Damen, 2020).
Circularity in Aerospace
Challenges and Opportunities: The aerospace industry faces unique challenges in implementing circular economy principles due to the stringent safety and performance requirements of aircraft. However, the industry also presents significant opportunities for enhancing resource efficiency and reducing waste.
Key Strategies
Lightweight Materials: Developing lightweight materials, such as carbon fiber composites, can improve fuel efficiency and reduce the environmental impact of aircraft. These materials offer high strength-to-weight ratios, reducing fuel consumption and greenhouse gas emissions during flight (Fielding et al., 2016).
Aircraft Component Recycling: Recycling aircraft components at the end of their service life can conserve valuable materials and reduce waste. This involves dismantling retired aircraft and recovering materials like aluminum, titanium, and composite fibers for reuse in new aircraft or other industries (Sefrin et al., 2016).
Remanufacturing and Refurbishment: Remanufacturing and refurbishing aircraft components extend their life and reduce the need for new parts. This approach conserves resources and offers economic benefits by reducing maintenance costs and downtime. Companies like Boeing and Airbus have established programs for remanufacturing and refurbishing aircraft engines and other components (Boeing, 2019).
Examples
Boeing’s EcoDemonstrator Program: Boeing’s EcoDemonstrator program tests and validates new technologies that improve the environmental performance of aircraft. The program includes initiatives for developing lightweight materials, enhancing fuel efficiency, and recycling aircraft components. Boeing’s commitment to sustainability demonstrates the potential for circularity in the aerospace industry (Boeing, 2019).
Airbus’ Recycling Initiatives: Airbus has implemented several initiatives to enhance the circularity of its operations. The company’s PAMELA (Process for Advanced Management of End-of-Life Aircraft) project focuses on the safe and efficient recycling of retired aircraft. Airbus also develops eco-friendly materials and designs aircraft for easy disassembly and recycling (Airbus, 2020).
Circularity in Energy
Challenges and Opportunities: The energy sector is critical for powering industries and economies, but traditional energy production methods often rely on non-renewable resources and generate significant greenhouse gas emissions. Implementing circular economy principles in the energy sector can enhance sustainability and reduce environmental impact.
Key Strategies
Renewable Energy: Transitioning to renewable energy sources, such as solar, wind, and hydroelectric power, is essential for reducing reliance on fossil fuels and minimizing environmental impact. Renewable energy systems can be designed with circularity in mind, incorporating recyclable materials and modular components (IRENA, 2020).
Energy Storage and Battery Recycling: Developing efficient energy storage systems, such as batteries, is crucial for integrating renewable energy into the grid. Recycling batteries at the end of their life can recover valuable materials like lithium, cobalt, and nickel, reducing the need for new mining and lowering environmental impact (Harper et al., 2019).
Circular Energy Systems: Implementing circular energy systems involves designing energy infrastructure that maximizes resource efficiency and minimizes waste. This includes district heating systems that utilize waste heat from industrial processes and cogeneration plants that produce electricity and heat simultaneously (IEA, 2019).
Examples
Tesla’s Energy Solutions: Tesla’s energy solutions, including solar panels, solar roofs, and energy storage systems, contribute to the circular economy by promoting renewable energy and efficient energy storage. Tesla’s battery recycling program ensures that materials from used batteries are recovered and reused in new batteries, enhancing resource efficiency (Tesla, 2020).
Ørsted’s Offshore Wind Farms: Ørsted, a global leader in renewable energy, develops and operates offshore wind farms that generate clean electricity. The company’s commitment to sustainability includes designing wind turbines with recyclable materials and implementing efficient maintenance practices to extend the life of components (Ørsted, 2020).
Policy and Regulatory Support
European Union Circular Economy Action Plan: The European Union has been a leader in promoting the circular economy through its Circular Economy Action Plan. This comprehensive policy framework aims to transform the EU’s economy into a more sustainable model by implementing measures to design out waste, keep products and materials in use, and regenerate natural systems. The Action Plan includes specific initiatives for sectors like plastics, textiles, electronics, and construction (European Commission, 2020).
China’s Circular Economy Promotion Law: China’s Circular Economy Promotion Law, enacted in 2008, provides a legal framework for promoting circular economy practices across various industries. The law encourages resource conservation, recycling, and sustainable consumption. It has led to significant investments in circular economy projects, including industrial parks, waste-to-energy facilities, and resource recovery centers (Geng et al., 2013).
Japan’s Sound Material-Cycle Society: Japan has implemented policies to establish a Sound Material-Cycle Society, focusing on reducing waste, promoting recycling, and encouraging the use of recycled materials. The country’s Basic Act for Establishing a Sound Material-Cycle Society outlines specific targets and measures for waste reduction and resource efficiency. Japan’s approach includes public awareness campaigns, incentives for recycling, and support for research and development in sustainable technologies (Nakamura, 2017).
Future Directions and Challenges
Scaling Up Circular Economy Practices: While there have been significant advancements in circular economy practices, scaling up these initiatives remains a challenge. It requires concerted efforts from governments, businesses, and consumers. Policies that incentivize circular practices, investments in sustainable technologies, and public education on the benefits of circularity are essential for broader adoption.
Overcoming Technological and Economic Barriers: The transition to a circular economy also faces technological and economic barriers. Developing new technologies for recycling and material recovery can be costly and require substantial investment. Additionally, changing existing production processes and supply chains to incorporate circular principles can be complex and resource-intensive. Addressing these barriers requires collaboration between industry stakeholders, research institutions, and policymakers.
Ensuring Social Equity: A just transition to a circular economy must also consider social equity. It is essential to ensure that the benefits of circularity are distributed fairly and that vulnerable communities are not disproportionately affected by the changes. Policies should include measures to support workers in transitioning industries, promote inclusive economic opportunities, and address potential social impacts.
Circularity in heavy industries such as building materials, automobiles, mining, chemicals, construction, shipbuilding, aerospace, and energy offers significant environmental, economic, and social benefits. By adopting circular economy principles, these sectors can reduce waste, conserve resources, and create more sustainable and resilient systems. Successful examples from companies like Renault, Tesla, Boliden, BASF, Damen, Boeing, and Ørsted demonstrate the potential for innovation and impact. However, scaling up circular practices requires overcoming technological and economic barriers, ensuring social equity, and fostering collaboration across all stakeholders. As the world moves towards a more sustainable future, circular economy practices will play a crucial role in achieving global sustainability goals.
References
1. Adams, K. T., Osmani, M., Thorpe, T., & Thornback, J. (2017). Circular economy in construction: Current awareness, challenges, and enablers. Proceedings of the Institution of Civil Engineers – Waste and Resource Management, 170(1), 15-24.
2. Andersen, A. B. (2001). Shipbreaking and the environment. Maritime Policy & Management, 28(2), 151-161.
3. Airbus. (2020). PAMELA Project: Sustainable aircraft recycling. Retrieved from [Airbus](https://www.airbus.com/newsroom/stories/pamela-project.html)
4. BASF. (2020). ChemCycling: Innovative chemical recycling of plastics. Retrieved from [BASF](https://www.basf.com/global/en/who-we-are/sustainability/we-drive-sustainable-solutions/circular-economy/chemcycling.html)
5. Boeing. (2019). EcoDemonstrator: Testing sustainable aviation technologies. Retrieved from [Boeing](https://www.boeing.com/commercial/ecoDemonstrator/)
6. Boliden. (2020). Sustainable mining practices at Aitik mine. Retrieved from [Boliden](https://www.boliden.com/operations/mines/boliden-aitik)
7. Braskem. (2019). Green Polyethylene: Renewable plastics from sugarcane. Retrieved from [Braskem](https://www.braskem.com.br/portal/green-polyethylene)
8. Caterpillar. (2020). Cat Reman: Benefits of remanufacturing. Retrieved from [Caterpillar](https://www.caterpillar.com/en/company/sustainability/remanufacturing.html)
9. Cohen, B., & Kietzmann, J. (2014). Ride on! Mobility business models for the sharing economy. Organization & Environment, 27(3), 279-296.
10. Damen. (2020). Modular ship design: Flexibility and sustainability. Retrieved from [Damen](https://www.damen.com/modular-ship-design)
11. Despeisse, M., Mbaye, F., Ball, P. D., & Levers, A. (2017). The emergence of sustainable manufacturing practices. Production Planning & Control, 23(5), 354-376.
12. Ellen MacArthur Foundation. (2019). Circular buildings toolkit. Retrieved from [Ellen MacArthur Foundation](https://www.ellenmacarthurfoundation.org/resources/apply/circular-design-toolkit/buildings)
13. European Commission. (2020). A new circular economy action plan for a cleaner and more competitive Europe. Retrieved from [European Commission](https://ec.europa.eu/environment/circular-economy/pdf/new_circular_economy_action_plan.pdf)
14. Fielding, J. P., Smith, H., & Walton, C. (2016). Lightweight materials for aircraft structures. Journal of Aerospace Engineering, 230(2), 229-240.
15. Geng, Y., Fu, J., Sarkis, J., & Xue, B. (2013). Towards a national circular economy indicator system in China: An evaluation and critical analysis. Journal of Cleaner Production, 23(1), 216-224.
16. Ghisellini, P., Cialani, C., & Ulgiati, S. (2016). A review on circular economy: The expected transition to a balanced interplay of environmental and economic systems. Journal of Cleaner Production, 114, 11-32.
17. Golev, A., Scott, M., Erskine, P. D., Ali, S. H., & Ballantyne, G. R. (2014). Rare earths supply chains: Current status, constraints and opportunities. Resources Policy, 41, 52-59.
18. Guglielmo, F. (2018). Modular construction: The future of the building industry? Construction Research and Innovation, 9(3), 64-67.
19. IEA. (2019). District heating: Delivering clean heat solutions. Retrieved from [IEA](https://www.iea.org/reports/district-heating)
20. IRENA. (2020). Renewable energy and circular economy: Synergies and opportunities. Retrieved from [IRENA](https://www.irena.org/publications/2020/Dec/Renewable-energy-and-circular-economy)
21. Kümmerer, K., Clark, J. H., & Zuin, V. G. (2020). Circular economy in the automobile industry: Best practices, enablers, and barriers. Sustainable Chemistry and Pharmacy, 18, 100322.
22. Lindhqvist, T. (2000). Extended Producer Responsibility in cleaner production: Policy principle to promote environmental improvements of product systems. IIIEE Reports.
23. Lund, R. T., & Hauser, W. M. (2019). Remanufacturing: An American perspective. International Journal of Advanced Manufacturing Technology, 102(1-4), 1495-1508.
24. Maersk. (2019). Responsible ship recycling: Setting new standards. Retrieved from [Maersk](https://www.maersk.com/news/articles/2019/09/20/maersk-to-recycle-ships-responsibly)
25. Nakamura, S. (2017). Japan’s transition to a Sound Material-Cycle Society. Journal of Material Cycles and Waste Management, 19(2), 1-12.
26. Ørsted. (2020). Ørsted’s commitment to sustainability: Building a green energy future. Retrieved from [Ørsted](https://orsted.com/sustainability)
27. Renault Group. (2021). Renault’s circular economy: Towards a more sustainable automotive industry. Retrieved from [Renault Group](https://www.renaultgroup.com/en/sustainability/circular-economy/)
28. Rio Tinto. (2021). Aluminium recycling and circular economy initiatives. Retrieved from [Rio Tinto](https://www.riotinto.com/sustainability/aluminium)
29. Schlüter, M., Post, P., & Lindner, K. (2014). Air lubrication: Reducing hull friction for energy efficiency. Journal of Marine Science and Technology, 19(3), 305-312.
30. Sefrin, R., Pischinger, S., & Meboldt, M. (2016). Recycling composite materials from aircraft: Opportunities and challenges. International Journal of Sustainable Engineering, 9(3), 165-174.
31. Siemens. (2019). Digital twin: The key enabler for Industry 4.0. Retrieved from [Siemens](https://new.siemens.com/global/en/company/stories/industry/digital-twin.html)
32. Tesla. (2020). Tesla battery recycling. Retrieved from [Tesla](https://www.tesla.com/blog/teslas-closed-loop-battery-recycling-program)
33. Thomson, H., Corbett, J. J., & Winebrake, J. J. (2016). Natural gas as a marine fuel. Energy Policy, 97, 603-615.
34. Van Damme, H., Mercier, S., & Le Bescop, P. (2020). Smart materials for sustainable construction. Materials & Design, 186, 108339.
35. Van Timmeren, A., & Jansen, S. (2016). Circular economy in the built environment: Park 20|20 case study. Sustainable Built Environment, 2(1), 93-105.